Fall protection equipment
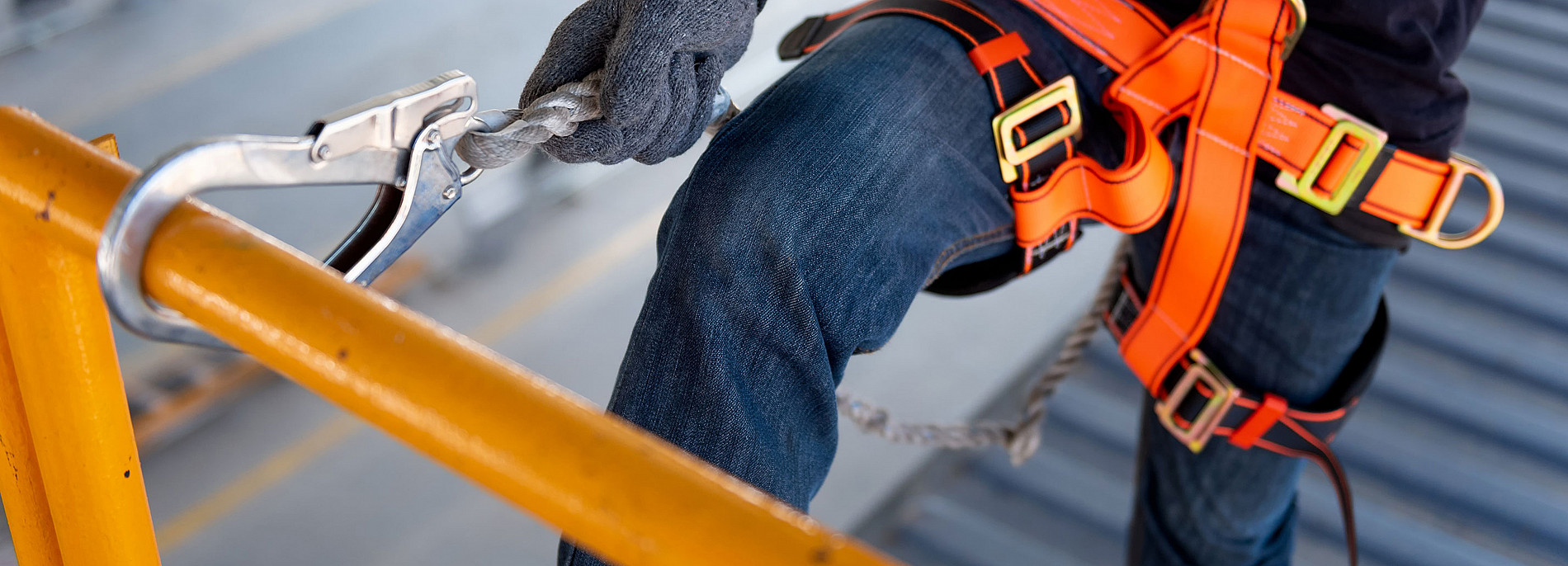
EKH sets itself the task of raising the bar when it comes to the safety of lifts and hoists. This page provides you with the latest information on those aspects which are important for newly purchased fall protection equipment, but also for equipment requiring periodic inspection.
What is fall protection equipment?
Fall protection equipment is categorised under personal protection equipment (PPE). This includes equipment, accessories or appurtenances which are intended to be worn or held by employees to protect themselves against health & safety hazards at work (with the exception of standard workwear, uniforms, sportswear, self-defence or deterrence material and portable equipment for detecting and identifying hazards and load factors).
European Directive on Personal Protection Equipment
Since April 1st 2018, a new European Directive on Personal Protection Equipment 89/686/EEC has been in force. Because fall protection equipment falls under the category of personal protection equipment, this directive also applies. One of the consequences is that liability, which had previously been restricted to the manufacturer, has now been extended to include importers and distributors. In addition, there is now the requirement that the load in the event of a fall must be under 600 kilograms.
User manuals for fall protection equipment
For all PPE – and that includes fall protection devices – there must be a user manual written in Dutch. The maintenance document must include complete information on the following:
- Product name;
- Name and address of the manufacturer or supplier;
- Serial number and/or lot number of the manufacturer;
- Year of manufacture (if possible, including the month);
- Date of purchase;
- An indication regarding the mandatory annual inspection;
- Space for comments after inspections;
- An indication of when the next annual inspection must take place.
It should be mentioned here that, in practice, no separate protocol is kept in respect of individual carabiners or closures. Neither do they always have a serial number or lot number from the manufacturer. So how can you satisfy the above requirement? As a user or owner, you yourself will have to decide whether fall protection devices require any additional identification and the way in which this fits into your system.
Markings for fall protection equipment
It is not just the maintenance document that needs to contain complete information. The personal protection equipment (and the separate components) itself must also be traceable. You can do this by specifying the following information on each device:
- Name of manufacturer and/or supplier;
- Type designation, for example: harness N-300-S;
- A CE-branding which is clearly visible, along with the reference number of the notified body which has reported the tests for admission. For example: CE-123;
- The European standard to which the product has been manufactured;
- The year (compulsory) and the month (explicitly recommended) of manufacture;
- The serial number of the manufacturer;
- The inspection sticker (which indicates the date by which the next inspection must take place);
- An insert with the unique number on a plate or label, but never on the product itself. Attach this to a spot where it is never in the way or presents a risk. If necessary, this can be done by stitching a plate with a ring on one of the slings of a harness (NB: stitch around, not affixed).
If the personal protection device affects health and/or safety, by preference this needs to come with harmonised pictograms.
What’s more, in practice, carabiners have no serial number. In this case, the best thing to do is copy the brands attached by the manufacturer on the certificate.
Testing of personal protection equipment (PPE)
EN-364 is the standard which prescribes testing. Testing is only carried out by a notified body before admission to the market, which means that testing by other parties has no status. In other words, you do not need to test personal protection equipment during the annual inspection. If there is no identification data available, the PPE cannot be approved, be traded, or be given to persons to use.
Inspection of fall protection equipment
The central reference point for inspecting personal protection equipment is the European standard NEN-EN 365. The three most important aspects in this are:
- Every system or every independently used component must be traceable by means of a manufacturer’s serial number or batch/lot number;
- Inspections of anything to do with personal fall protection, must take place at least once every 12 months;
- According to the European standard NEN-EN-365, only an expert authorised by the manufacturer is permitted to inspect specialist fall protection equipment, which must be compulsorily opened for inspection. If prescribed by the manufacturer, maintenance also needs to be carried out. For simple PPE, a person who can demonstrate they are qualified to do so can inspect the devices.
However, EKH stipulates that a person who is qualified to inspect simple PPE should, as a minimum, have followed a product training session with at least one manufacturer or specialist supplier. This person must also be able to demonstrate that this know-how is maintained, for example, by following regular refresher courses. We stipulate this because obtaining authorisation for all brands of simple PPE is not seen as feasible in practice.
Fall protection equipment is not tested during inspections, but checked visually and assessed on the basis of its functioning. If in any doubt, the material should therefore always be rejected. If an item of equipment is not complete, will not function properly, or is not of the right quality, this should be reported and registered.
Replacement periods
There are no strict replacement periods set down in law or in the standards. These are determined by each manufacturer and prescribed per product. These can vary from between 3 to even more than 10 years. This period acts as the guiding principle.
Following a fall, lines and slings, harnesses, fall arrestors, metal fittings and carabiners and fall arrest blocks must be immediately taken out of use and replaced. In the event of fall arrest blocks, these must be submitted to an authorised party for approval.